NEWS | BY KIVNON
The crunch on warehouse and other material-handling operations, and how Automated Guided Vehicles technology can help
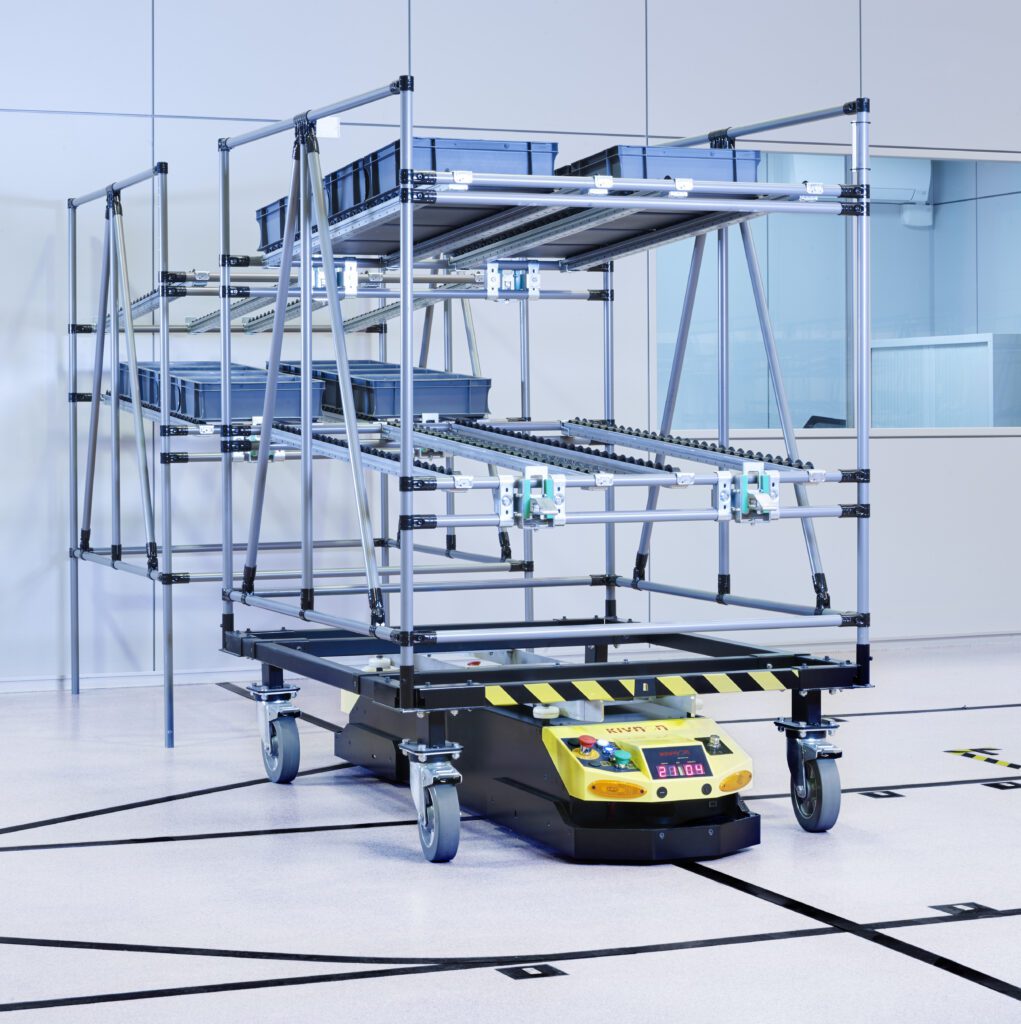
The pandemic both reduced the available workforce and accelerated online sales. Warehouse operations grew and had to handle increased volume with fewer employees. Prior to Covid-19, the answer to this problem was to hire more fork truck drivers. Now, companies have difficulty finding trained fork truck operators. These circumstances caused many companies to take a second look at a technology that has been around for a long time: automated guided vehicles (AGVs).
Cost-effective AGVs solutions
Before Covid-19, the ROI for AGVs only made sense for large manufacturing and warehouse operations. In many cases, these larger facilities still needed to run two or three shifts to cost-justify the AGV automation expense. That has changed; reasonably priced AGVs are now available to smaller operations. Ironically, there is now a backlog on delivering orders of basic fork trucks.
Distinctions of AGVs, AGCs, and AMRs
AGVs typically come in two styles—fork style AGVs or tugger AGVs—and they tend to be larger units. Automated guided carts (AGCs) are smaller but have the same functionality. Autonomous mobile robots (AMRs) are the newer kids on the block and more focused on e-commerce. A basic difference between AGV/AGC and AMRs is that the former are guided along a fixed path, whereas the latter use radar and other sensing devices—i.e., intelligent navigation—to determine their path. There are also different rules regarding safety and how they operate.
Capturing the automation trend in Automated Guided Vehicles sector
Automation can only fulfil its promised features, advantages, and benefits if it’s cost-effective, available for immediate delivery, and maintains quality and safety rigour. Tried and tested for decades, robotic magnetic guided, or magnetic tape AGCs, have proven effective for the vast majority of market demands. This simple, cost-effective navigation technology is ideal for warehouse e-commerce operations. Companies apply a special magnetic tape to the floor, and the cart follows along the tape.
Magnetic tape is easy to change, so modifications can be made as needed. If the tape is damaged, it’s easy to repair.
The tape can be supplemented with RFID tags that can give simple instructions to the AGV. They can be used along with new apps such as Flex Tag that can be accessed on an Android phone.
An example of this technology is AGVs from Kivnon. A two-vehicle system, with automatic charging, it can run 24/7 and is a fully automated turnkey system that costs around $100K. Of course, you can get bigger units and more complex configurations. Compared to hiring (if one can) and training one fork truck driver, this is a fairly low-cost, entry-level system for automation.
Capturing the automation trend
From a financial perspective, calculating ROI is critical. Running only one shift makes rapid ROI slower and more problematic. Conversely, when operating in a high-wage area with two or three shifts running five or more days a week, payback happens much sooner.
Original post from: Quality Digest